3D Printing and Its Influence on PCB Design Services
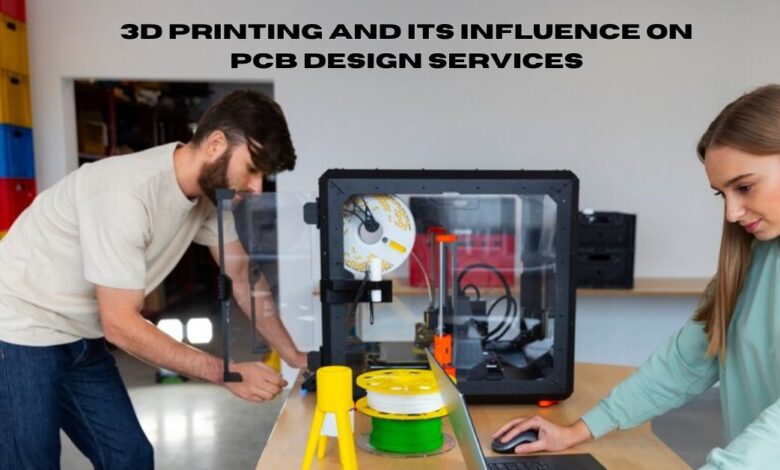
The convergence of 3D printing technology and PCB (Printed Circuit Board) design services is revolutionizing the electronics industry, offering new possibilities for innovation, customization, and efficiency. As 3D printing continues to advance, it significantly influences how PCBs are designed, prototyped, and manufactured, ushering in a new era of technological capabilities and design flexibility.
The Evolution of PCB Design
Traditionally, PCB design has involved a multi-step process that includes schematic capture, layout design, prototyping, testing, and finally, mass production. This process can be time-consuming and costly, particularly during the prototyping phase where multiple iterations may be required to perfect the design. PCB design services have always focused on optimizing these processes to improve efficiency and reduce time-to-market.
The Advent of 3D Printing in Electronics
3D printing, or additive manufacturing, builds objects layer by layer from digital models, offering unparalleled flexibility in design and manufacturing. In the context of PCB design, 3D printing introduces several transformative benefits:
- Rapid Prototyping: One of the most significant advantages of 3D printing in PCB design is the ability to produce prototypes quickly. Traditional methods can take days or weeks to produce a prototype, whereas 3D printing can accomplish this in a matter of hours. This rapid prototyping capability allows designers to test and iterate more efficiently, speeding up the development process.
- Complex Geometries: 3D printing allows for the creation of complex geometries that would be difficult or impossible to achieve with traditional manufacturing methods. This capability is particularly beneficial for designing PCBs for applications with unconventional shapes or space constraints, such as wearable devices and compact electronics.
- Integrated Functionality: With 3D printing, it is possible to integrate various functionalities directly into the PCB. For example, antennas, sensors, and even batteries can be embedded within the layers of the PCB, reducing the need for additional components and assembly steps. This integration enhances the overall performance and reliability of the final product. Additionally, embedded software development services can further optimize these integrated systems by providing customized firmware and software solutions that ensure seamless operation and enhanced functionality.
- Material Innovation: Advances in 3D printing materials are expanding the possibilities for PCB design. Conductive inks and flexible substrates enable the creation of flexible and stretchable PCBs, opening up new applications in fields like wearable technology, medical devices, and IoT (Internet of Things).
- Cost Efficiency: For low-volume production and custom designs, 3D printing can be more cost-effective than traditional manufacturing methods. It eliminates the need for expensive tooling and setup costs, making it an attractive option for startups and small businesses looking to bring innovative products to market.
Practical Applications and Case Studies
Several industries are already leveraging the benefits of 3D printing in PCB design services:
- Aerospace:The aerospace industry requires highly reliable and lightweight electronic components. 3D printing allows for the integration of complex, lightweight structures with embedded electronics, improving performance and reducing weight. Moreover, 3D CAD services play a crucial role in designing these intricate structures, ensuring precise modeling and optimization for both functionality and manufacturability.
- Medical Devices: In the medical field, custom-fit devices and implants are crucial. 3D printing enables the production of patient-specific devices with integrated electronic components, enhancing the functionality and effectiveness of medical devices.
- Consumer Electronics: Wearable technology, such as fitness trackers and smartwatches, benefits from 3D-printed PCBs that conform to the body and integrate multiple functionalities within a single, compact device.
Challenges and Future Prospects
While 3D printing presents numerous advantages, it also comes with challenges that need to be addressed:
- Material Limitations: Although there have been significant advancements in conductive and dielectric materials for 3D printing, they still lag behind traditional materials in terms of electrical performance and durability.
- Standardization and Quality Control: Ensuring consistency and reliability in 3D-printed PCBs is crucial for widespread adoption. Standardized processes and rigorous quality control measures are necessary to meet industry standards.
- Scalability: While 3D printing is excellent for prototyping and low-volume production, scaling up for mass production remains a challenge. Integrating 3D printing with traditional manufacturing processes could offer a hybrid solution to this issue.
Looking ahead, the continued development of 3D printing technology and materials will likely overcome these challenges. Innovations such as multi-material 3D printing, higher resolution printing, and improved material properties will expand the capabilities and applications of 3D-printed PCBs.
Conclusion
3D printing is profoundly influencing PCB design services, offering new levels of flexibility, efficiency, and innovation. By enabling rapid prototyping, complex geometries, integrated functionality, and cost-effective production, 3D printing is transforming how PCBs are designed and manufactured. As the technology continues to evolve, it holds the promise of further revolutionizing the electronics industry, paving the way for more advanced, customized, and high-performing electronic devices. Embracing 3D printing in PCB design is not just an option but a strategic imperative for staying competitive in the fast-paced world of technology.