Key Considerations for Torque Wrench Calibration in Houston
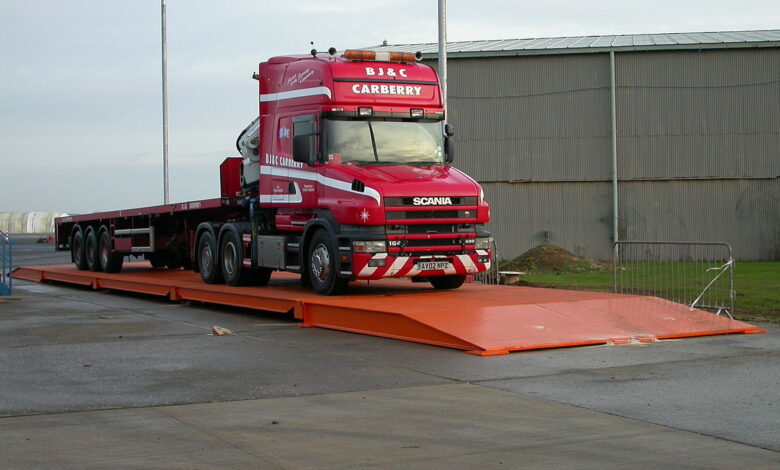
Calibration of torque wrenches is a critical aspect of ensuring precision, accuracy, and reliability in industrial applications.
Industrial Scale & Measurement, a trusted provider in Houston, offers key considerations for torque wrench calibration to help businesses maintain optimal performance and compliance. From understanding the importance of calibration to navigating regulations and standards, this article explores the benefits of working with certified calibration services, common challenges in calibration procedures, best practices, and the impact of calibration on tool performance.
By examining cost considerations, ROI, and real-world case studies, businesses can gain insights into the value of torque wrench calibration for enhancing operational efficiency and maintaining quality standards.
Understanding the Role of Torque Wrenches in Industrial Applications
Torque wrenches are like the unsung heroes of industrial settings, ensuring that bolts and nuts are tightened just right to keep things running smoothly. Think of them as the precision tools that prevent catastrophic equipment failures or leaks by applying the perfect amount of twist.
Significance of Accuracy and Precision in Torque Applications
You wouldn’t want a loose screw in your favorite IKEA bookshelf, right? The same goes for industrial machinery – accuracy and precision are non-negotiable. Calibrating torque wrenches ensures that they are on point, avoiding under or over-tightening that could spell disaster.
Regulations and Standards for Torque Wrench Calibration
Just like speed limits keep the roads safe, industry standards and guidelines exist to maintain the integrity of torque applications. These rules provide a roadmap for proper calibration practices that keep everything in check.
Compliance Requirements for Torque Wrench Calibration in Houston
In Houston, where everything seems bigger, torque wrench calibration is no exception. Compliance requirements ensure that businesses in the area play by the rules, preventing any loose ends when it comes to tightening bolts and ensuring safety.
Benefits of Working with a Certified Calibration Service
Imagine entrusting your torque wrench to a shady character named Larry in a back alley versus a certified calibration service. Expertise and accreditation are the badges of honor that assure you’re in good hands, with professionals who know their torque from their twist.
Enhanced Reliability and Consistency in Calibration Results
Consistency is key, especially when it comes to torque wrench calibration. Working with certified services guarantees that your wrenches will be calibrated with the same precision each time, leaving no room for doubt or second-guessing.
Common Challenges in Torque Wrench Calibration
Just like baking a soufflé, a lot can go wrong if you don’t follow the recipe. Factors like environmental conditions or wear and tear can impact torque wrench calibration, throwing off the perfect balance of twist and turn.
Troubleshooting Calibration Issues and Errors
When your torque wrench goes rogue, it can be like dealing with a stubborn toddler – frustrating and confusing. Troubleshooting calibration issues requires detective work to pinpoint the source of errors, ensuring that your wrenches are back in line and ready to tackle any twisty task.
Calibration Procedures and Best Practices
Step-by-Step Calibration Process for Torque Wrenches
Calibrating your torque wrench is like giving it a tune-up – essential for accuracy and performance. Step one: Get a reputable calibration service. Step two: Follow their specific procedure, usually involving applying known torque to the wrench and adjusting it accordingly. Step three: Get ready to tighten bolts with newfound precision!
Implementing Best Practices to Ensure Accurate Calibration Results
To keep your torque wrench singing sweetly, store it properly (not in that dark, dusty corner!). Regular recalibration is crucial. Treat it with care – dropping a torque wrench is like breaking a musician’s favorite guitar. And always follow manufacturer guidelines. Remember, a happy torque wrench is an accurate torque wrench!
Impact of Calibration on Tool Performance and Accuracy
Improving Tool Performance through Regular Calibration
Calibration isn’t just a chore – it’s a performance enhancer! Just like a workout for your wrench, regular calibration ensures it stays in top form. Say goodbye to loose bolts and hello to precision engineering. Your torque wrench will thank you by tightening things up like never before.
Ensuring Accuracy and Consistency in Torque Applications
Calibration isn’t just about numbers – it’s about trust. Knowing your torque wrench is accurate means you can trust it to get the job done right every time. Consistency is key in torque applications – no one wants a loose cannon wrench messing up their machinery. Calibrate, trust, tighten – in that order.
Cost Considerations and Return on Investment
Evaluating the Costs Associated with Torque Wrench Calibration
Yes, calibration comes with a price tag, but think of it as an investment in precision. Consider the cost of a faulty torque wrench – mistakes, rework, and potentially damaged equipment. Calibration costs are a small price to pay for peace of mind and accurate results.
Calculating the ROI of Investing in Calibration Services
Calculating ROI for torque wrench calibration? Simple. Take the cost of calibration, subtract the potential costs of inaccuracy, rework, or damage, and voilà – there’s your return on investment. Invest in calibration today, save on headaches tomorrow. It’s a win-win tightening situation.
Success Stories in Torque Wrench Calibration
Real-World Examples of Improved Performance Post-Calibration
From Houston to Helsinki, torque wrench calibration success stories abound. Tightening bolts with newfound accuracy, reducing errors, and improving efficiency – it’s like a torque wrench transformation. Real-world results speak louder than words, and post-calibration performance speaks volumes.
Testimonials from Clients on the Benefits of Calibration Services
Clients singing praises about torque wrench calibration? You betcha. From saving time and money to preventing costly mistakes, the benefits are crystal clear. Testimonials don’t lie – calibrate, tighten, succeed. Trust the wrench, feel the power, and join the calibration fan club today!
Conclusion
In conclusion, torque wrench calibration plays a crucial role in ensuring the accuracy and reliability of industrial processes. By adhering to regulations, working with certified calibration services, and implementing best practices, businesses in Houston can optimize tool performance and maintain consistency in their operations. The investment in calibration services not only enhances accuracy but also offers long-term benefits in terms of improved efficiency and reduced downtime. Through a proactive approach to calibration and a focus on quality, companies can achieve operational excellence and uphold standards of excellence in torque applications.
Why is torque wrench calibration important?
A: Torque wrench calibration is essential to ensure accurate and reliable torque measurements, which are critical for the safety and performance of industrial machinery and components.
How often should torque wrenches be calibrated?
A: The frequency of calibration depends on factors such as usage frequency, application requirements, and industry standards. Generally, torque wrenches should be calibrated at regular intervals, typically annually or as recommended by the manufacturer.
What are the consequences of using uncalibrated torque wrenches?
A: Using uncalibrated torque wrenches can lead to inaccuracies in torque application, resulting in faulty assembly, compromised product quality, and potential safety hazards in industrial settings.
Can in-house calibration be as effective as outsourcing to a professional service?
A: While in-house calibration can be feasible for some businesses, outsourcing to a professional Industrial Scale & Measurement offers expertise, accreditation, and specialized equipment that ensure precise and consistent calibration results, ultimately enhancing tool performance and operational efficiency.