Securing Success: Innovations in Workholding Fixture Design
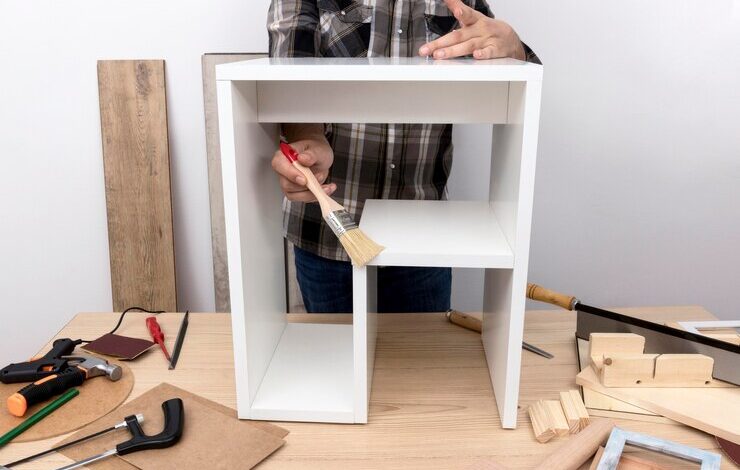
In the fast-paced world of manufacturing, precision and efficiency are key. Workholding fixture design plays a crucial role in achieving these goals. By securely holding parts during machining, innovative workholding fixtures ensure accuracy and consistency. This article examines the importance of workholding fixture design, its benefits, and recent innovations that are driving success in the industry.
The Role of Workholding Fixture Design
Workholding fixtures are essential for maintaining precision in machining processes. Standard fixtures often cannot handle unique or complex parts effectively. Innovative workholding fixture design tailors solutions to fit the exact dimensions and requirements of each part. This ensures a secure hold and precise machining, enhancing product quality and reducing waste.
Benefits of Advanced Workholding Fixtures
Here are some benefits of advanced workholding fixtures:
- Improved Precision: Advanced workholding fixtures minimize movement and vibration. This results in higher accuracy and consistency in machining, leading to superior product quality.
- Enhanced Efficiency: Custom-designed workholding fixtures streamline the machining process. They reduce setup times and improve workflow, allowing for faster production cycles and increased output.
- Cost Reduction: By ensuring precise machining, innovative workholding fixtures decrease the likelihood of errors and defects. This leads to less material waste and lower costs associated with rework and scrap.
Innovations in Workholding Fixture Design
Recent innovations in workholding fixture design have transformed manufacturing processes. These innovations include modular fixtures, flexible clamping systems, and automated solutions.
- Modular Fixtures: Modular fixtures allow for quick reconfiguration, making them ideal for small batch production and prototyping. They offer flexibility and adaptability, ensuring efficient machining for various parts.
- Flexible Clamping Systems: Flexible clamping systems use adaptable components to hold parts securely. They can accommodate different shapes and sizes, providing a versatile solution for complex machining tasks.
- Automated Workholding Solutions: Automation has revolutionized workholding fixture design. Automated solutions integrate with CNC machines, enabling precise and repeatable clamping without manual intervention. This enhances productivity and reduces human error.
Choosing the Right Workholding Fixture
Selecting the right workholding fixture involves understanding the specific needs of the machining process. Factors such as part geometry, material, and machining operations must be considered. Collaborating with experienced engineers can help in designing and implementing the most effective workholding fixture for your needs. Additionally, considering the frequency of part changeovers and production volume can further enhance the efficiency and suitability of the chosen fixture. This comprehensive approach ensures that the fixture meets immediate requirements and adapts to future needs, maximizing productivity and cost-effectiveness.
Conclusion
Innovations in workholding fixture design are vital for modern manufacturing, providing the precision and efficiency needed to produce high-quality products. By tailoring fixtures to specific needs, manufacturers can optimize processes, reduce waste, and increase productivity. Investing in advanced workholding fixtures is a strategic move that can yield significant long-term benefits, ensuring that your manufacturing operations run smoothly and efficiently.
In an industry where precision and efficiency are critical, innovative workholding fixture design stands out as a key component of success. These fixtures not only improve the quality and consistency of products but also contribute to overall operational excellence.